提升硫自養濾料脫氮效率的綜合調控策略
發布時間:
2025-06-30
硫自養濾料脫氮技術因其無需外加碳源、運行成本低等優勢,在廢水處理領域備受關注。然而,其效率受微生物活性、反應條件、濾料性能及工藝設計等多因素影響。本文從實際應用角度出發,提出系統性優化方法,以提升脫氮效率。
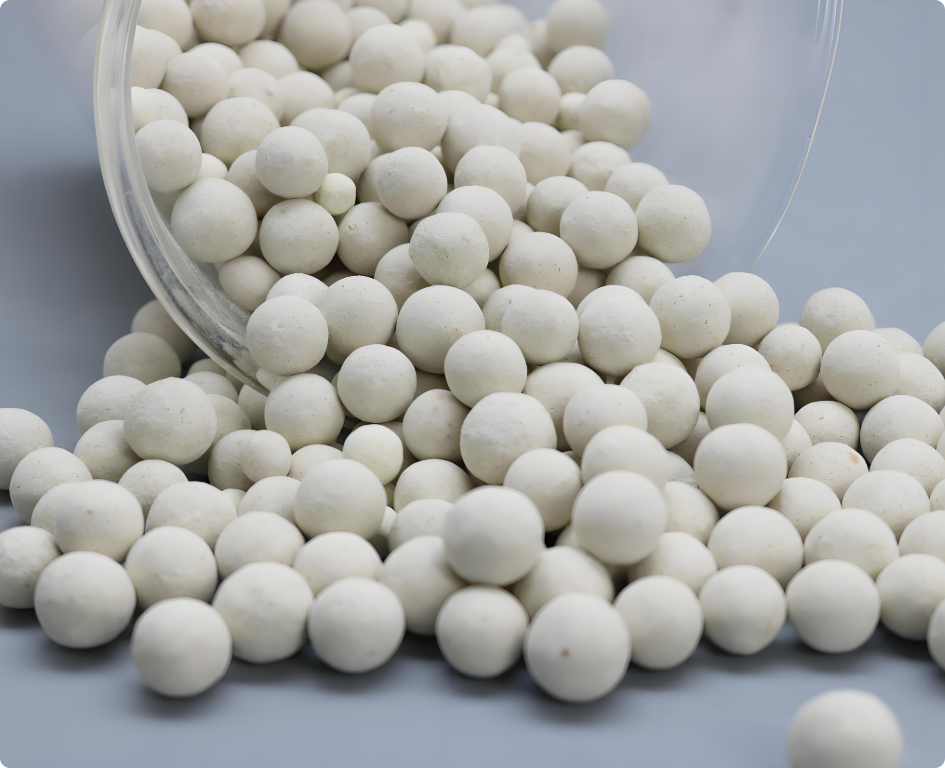
一、優化微生物生長環境
硫氧化細菌(如硫桿菌)是脫氮過程的核心,需為其創造適宜的生長條件。
pH調控:細菌最適pH為6.5~8.0。酸性廢水可投加NaOH或CaO調節,堿性廢水可引入CO?,避免劇烈波動影響酶活性。
溶解氧控制:硫自養反硝化需缺氧環境(DO<0.5 mg/L)。可通過厭氧反應器設計或分段曝氣實現,避免氧氣競爭電子供體。
硫源供給:單質硫(S?)經濟但反應慢,硫化物(如Na?S)反應快但需防H?S毒性。理論硫氮比為2.86:1(以S?計),需根據實際水質調整。
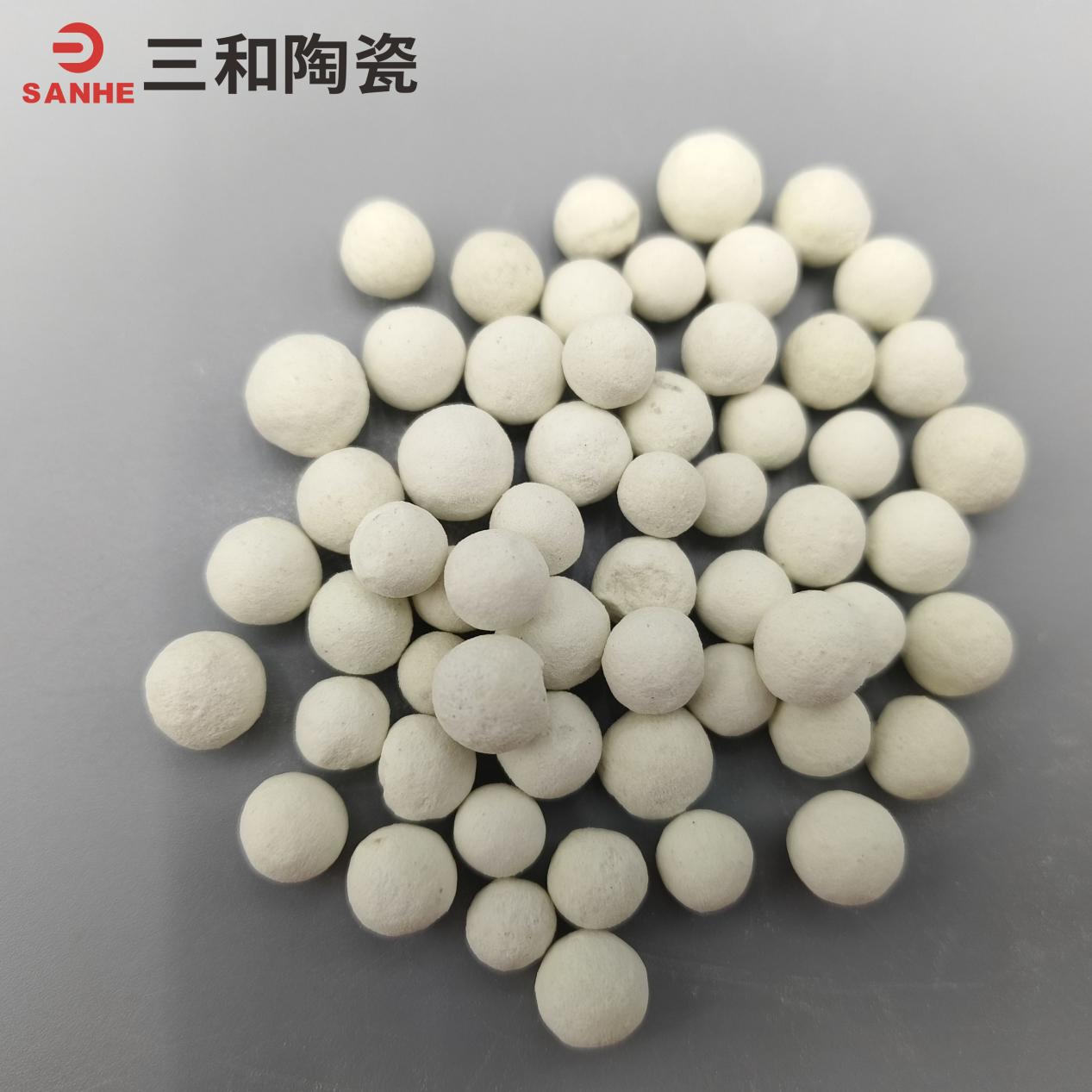
二、改進濾料性能與結構
濾料是微生物附著的載體,直接影響傳質效率和生物膜穩定性。
材料選擇:優先選用火山巖、陶粒等高比表面積(50~100 m2/g)且耐腐蝕的材料,避免金屬濾料被硫化物侵蝕。
粒徑與填充優化:小粒徑(2~5 mm)適合低懸浮物廢水,大粒徑(5~10 mm)可防堵塞。建議分層填充,并定期反沖洗(每周1~2次)防止堵塞。
生物膜培養:啟動階段采用低負荷進水,逐步提升濃度;運行中避免水力沖擊,通過回流或脈沖進水維持穩定性。
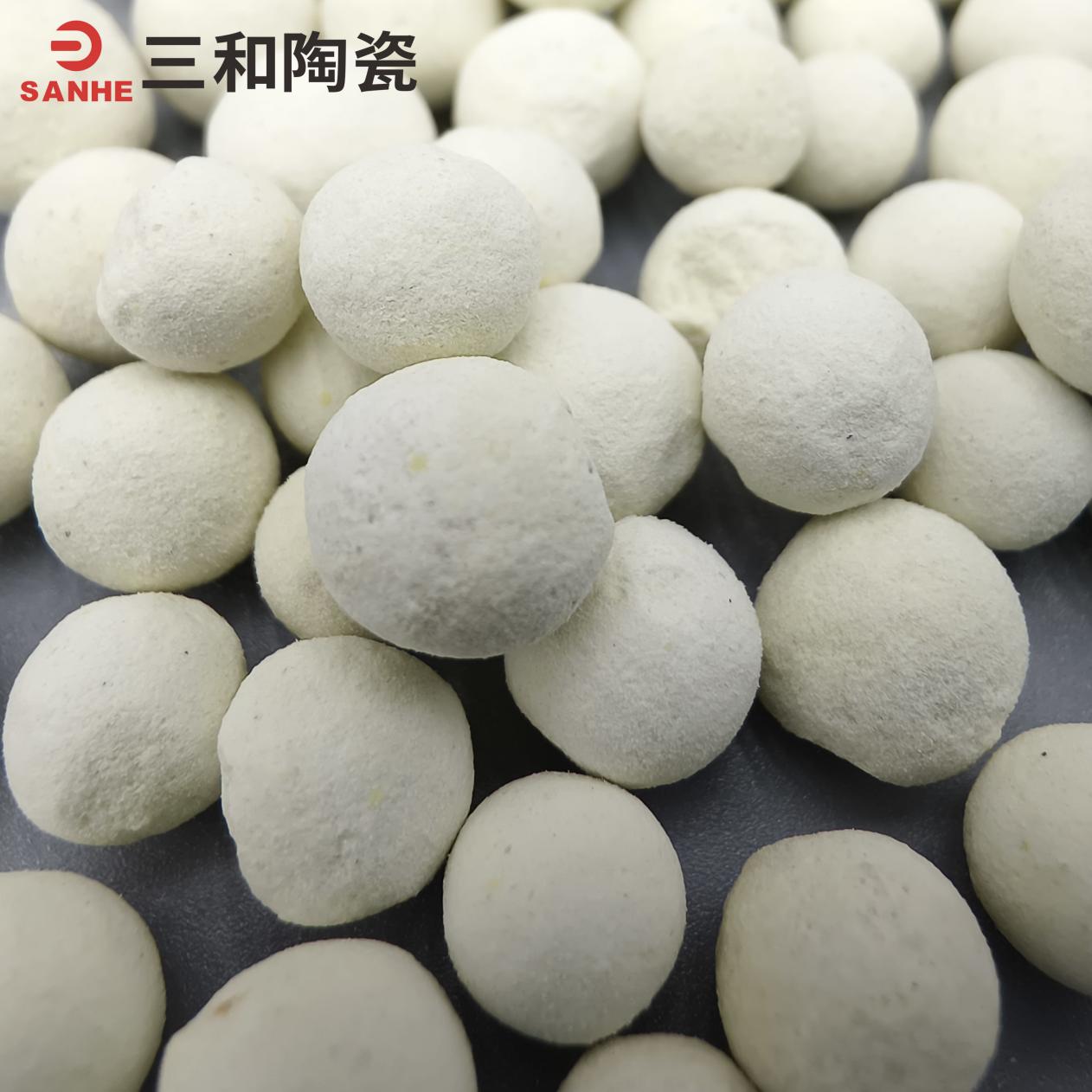
三、優化工藝運行參數
工藝參數的精準控制是高效脫氮的關鍵。
水力停留時間(HRT):通常設為6~12小時,過短會導致反應不充分,過長易引發污泥膨脹。
溫度管理:適宜溫度為20~35℃。低溫(<15℃)會抑制細菌活性,需采取保溫或加熱措施。
動態監測:實時檢測NO??-N、pH、DO及S2?濃度,通過自動反饋調節硫源投加量和反沖洗頻率。
四、強化傳質與反應設計
改善傳質效率:采用流化床或移動床工藝增強混合,或添加腐殖酸等電子介體加速反應。
分段反應器設計:多級串聯可分級脫氮,第一級高負荷快速去除NO??-N,后續級深度處理并減少硫殘留。
五、案例與注意事項
某化工廠通過優化濾料(火山巖+硫顆粒)、控制pH=7.5、HRT=8小時,將脫氮效率從60%提升至90%以上。需注意副產物SO?2?的后續處理,必要時串聯生物除硫工藝。
結語
硫自養脫氮效率的提升需多維度協同調控。通過優化微生物環境、濾料性能、工藝參數及傳質條件,可實現高效穩定運行,同時降低硫源損耗與成本。實際應用中需結合水質特點靈活調整,以達到最佳處理效果。
下一頁:
推薦新聞
2025-07-02
2025-07-01
2025-06-30
2025-06-25
2025-06-24
分享到